One of the key tools we use to boost warehouse performance is the FACTS framework, which stands for Flow, Access, Capacity, Trace, and Safety. Flow refers to optimizing the movement of products through the warehouse to reduce unnecessary handling and costs. Access is about ensuring picking areas are clear and easily navigable. Capacity focuses on using the right storage systems to maximize efficiency. Trace emphasizes accurate inventory tracking, while Safety underpins all operations…
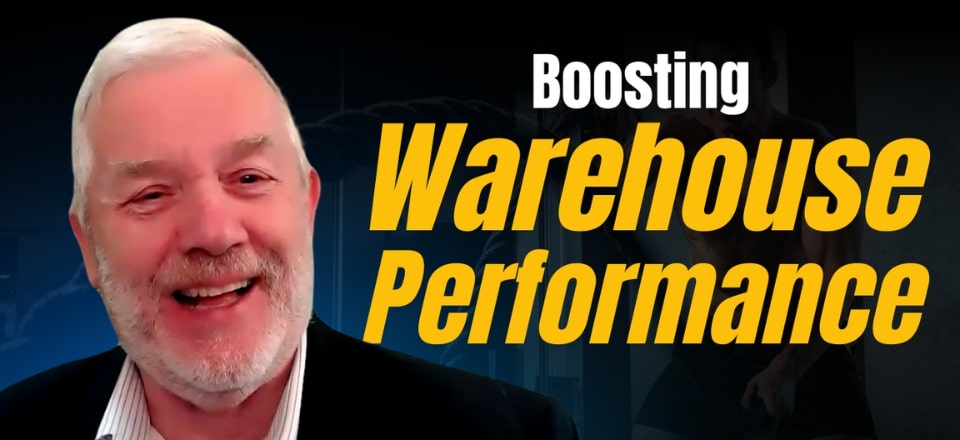